Automatic 20kg Flour Food Valve Bag Packing Machine with Ultrasonic Sealing Device 2
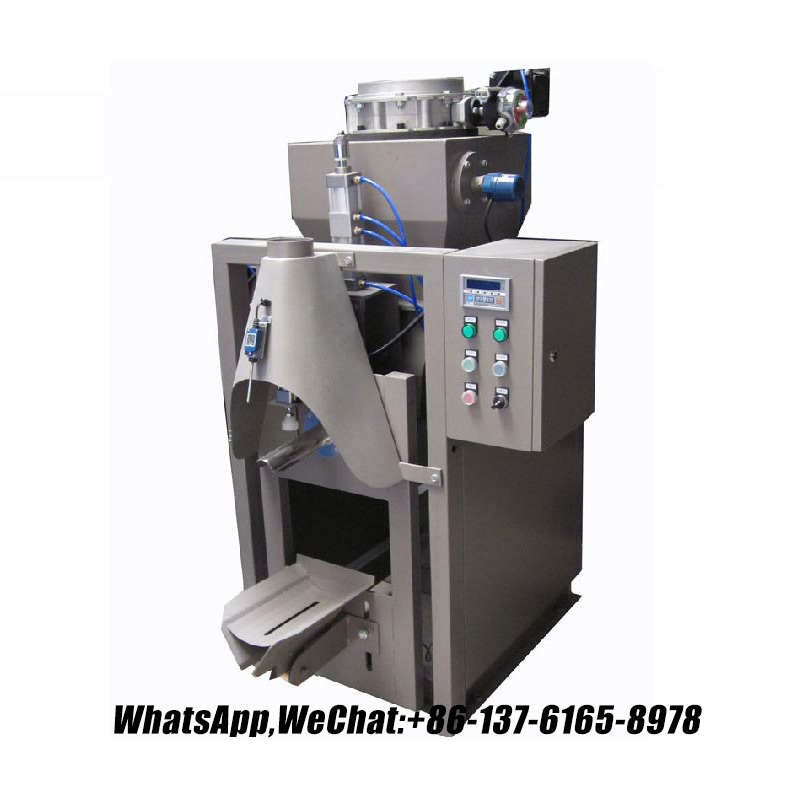
An Automatic 20kg Flour Food Valve Bag Packing Machine with Ultrasonic Sealing Device is designed for efficient, precise, and hygienic packaging of flour and other food powders into valve bags. Below is a detailed overview of its features, benefits, applications, and key considerations:
Key Features:
Automated Operation:
Fully Automatic System: From weighing, filling, sealing, to discharging, the machine operates with minimal human intervention.
PLC Control: Programmable logic controller ensures precise and repeatable filling cycles.
Touchscreen Interface: User-friendly HMI (Human-Machine Interface) for easy operation and parameter adjustments.
Precision Weighing and Filling:
High-Accuracy Load Cells: Ensures ±10-50g accuracy for 20kg bags, reducing product wastage.
Vibration-Free Filling: Prevents dust emissions and maintains product integrity.
Adjustable Filling Speeds: Prevents overfilling or spillage, especially for fine powders like flour.
Ultrasonic Sealing Device:
Hermetic Seal: Ultrasonic technology creates a secure, airtight seal on valve bags, preventing moisture and contaminants.
No Heat Generation: Unlike thermal sealing, ultrasonic sealing avoids overheating the product, preserving quality.
Tamper-Evident Seals: Enhances security and freshness during storage and transportation.
Valve Bag Compatibility:
PE or PP Valve Bags: Suitable for standard 20kg valve bags with spouts for easy pouring.
Dust-Tight Design: Minimizes product loss and keeps the work area clean.
Hygienic Design:
Stainless Steel Construction: 304/316 stainless steel contact parts for corrosion resistance and food safety.
Easy Cleaning: Smooth surfaces and removable components simplify sanitation.
Food-Grade Materials: Compliant with food safety standards (e.g., CE, FDA, NSF).
Dust Control:
Integrated Dust Extraction: Connects to a dust collection system to minimize airborne particles.
Sealed Hopper and Auger: Prevents dust leakage during filling.
Safety Features:
Emergency Stop Button: Halts operation immediately in case of emergencies.
Overload Protection: Prevents motor damage from excessive load.
Interlocking Guards: Protects operators during maintenance.
Customizable Options:
Nitrogen Blanketing: Inert gas purging to preserve product freshness and prevent oxidation.
Date/Batch Coding: Optional printers for labeling bags with expiration dates or batch numbers.
Conveyor Systems: Automates bag transport to downstream processes like palletizing or sealing.
Efficiency:
High Throughput: Capable of packing 10-20 bags per minute, depending on the model.
24/7 Operation: Designed for continuous use with minimal downtime.
Benefits:
Precision and Consistency: Accurate filling reduces product waste and ensures uniform bag weights.
Hygiene and Safety: Stainless steel construction and dust control meet food safety standards.
Efficiency: Automated operation increases productivity and reduces labor costs.
Product Integrity: Ultrasonic sealing preserves freshness and prevents contamination.
Versatility: Suitable for flour, sugar, powdered milk, spices, and other food powders.
Low Maintenance: Robust design and easy-to-clean components minimize downtime.
Applications:
Flour Milling: Packaging wheat flour, rice flour, or cornmeal into 20kg valve bags.
Food Processing: Bagging powdered milk, baking mixes, spice blends, or instant beverages.
Feed Manufacturers: Packing animal feed powders or pellets.
Chemical Industries: Packaging non-hazardous powders like talcum powder or detergents.
Pharmaceuticals: Bagging powdered medications or dietary supplements.
Operation Steps:
Bag Placement:
An empty valve bag is manually placed on the conveyor or automatically fed by a bagging system.
Weighing and Filling:
The machine weighs the required amount of flour using load cells and fills the bag through an auger or gravity spout.
Ultrasonic Sealing:
The valve bag spout is sealed using the ultrasonic sealing device, creating a secure, tamper-evident closure.
Discharging:
The filled and sealed bag is discharged onto a conveyor for further handling (e.g., labeling, palletizing).
Cleanup:
Dust extraction systems and sealed components minimize product residue, keeping the machine clean.
Considerations When Purchasing:
Product Characteristics: Ensure the machine is suitable for your specific powder (e.g., fineness, flowability, moisture sensitivity).
Output Requirements: Choose a model with the appropriate speed (bags per minute) for your production needs.
Bag Type: Verify compatibility with your valve bags (e.g., PE, PP, or custom sizes).
Hygiene Standards: Check compliance with food safety regulations (e.g., FDA, CE, NSF).
Customization Needs: Consider additional features like nitrogen blanketing, coding systems, or integration with other equipment.
Maintenance and Training: Ensure the machine is easy to clean and maintain, and that operators receive proper training.
Budget: Automatic machines with ultrasonic sealing are more expensive than manual or semi-automatic options but offer long-term efficiency gains.
Why Choose This Machine?
This machine combines precision, hygiene, and efficiency, making it ideal for packaging flour and other food powders. The ultrasonic sealing device ensures hermetic closures, while the automated system reduces labor costs and minimizes product waste. It’s a reliable solution for food manufacturers seeking scalable, high-quality packaging.
Immediate Order:
Website: https://www.glzon.com/product/drumfillingmachines-en.html
China Manufacturing Co Ltd.: https://fillingmachinecn.en.made-in-china.com
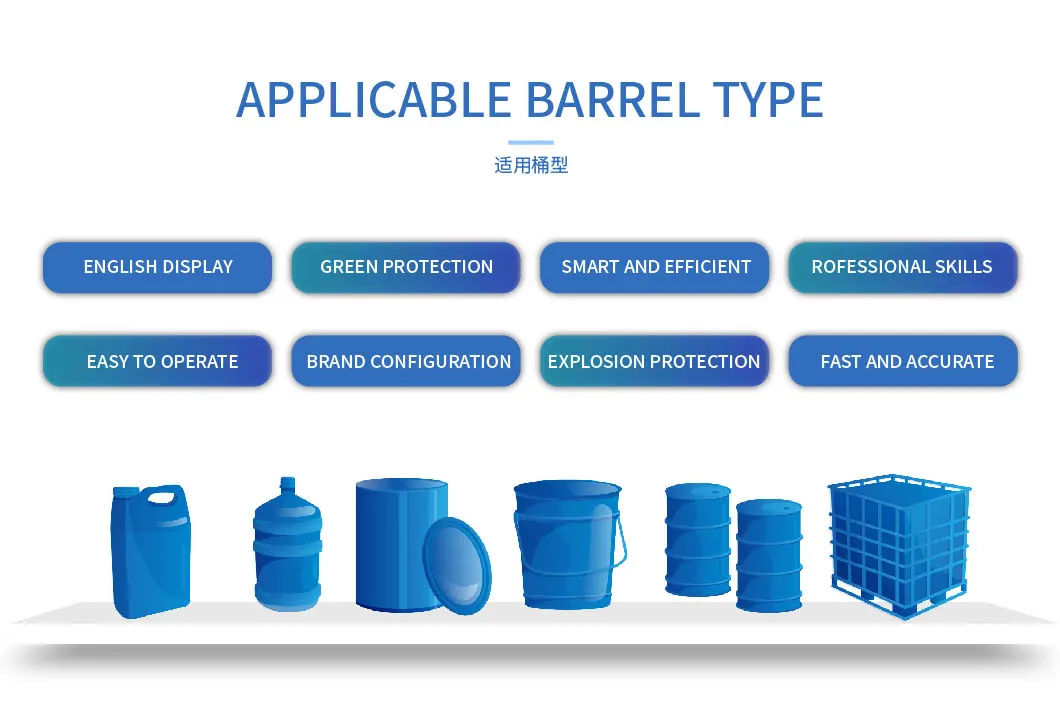
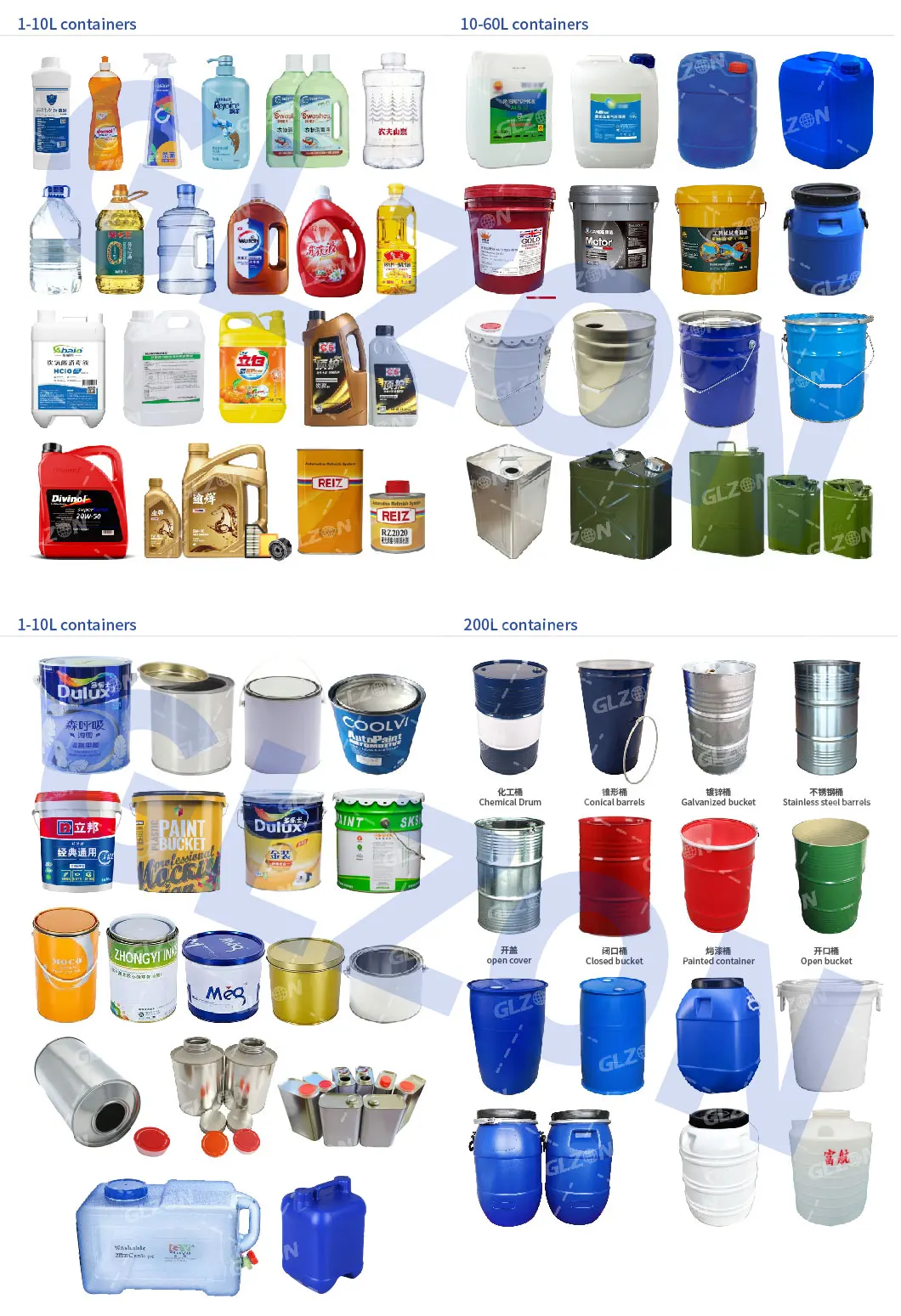
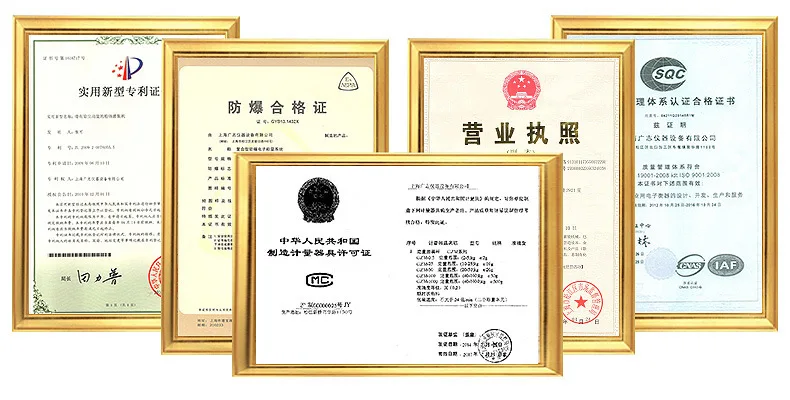
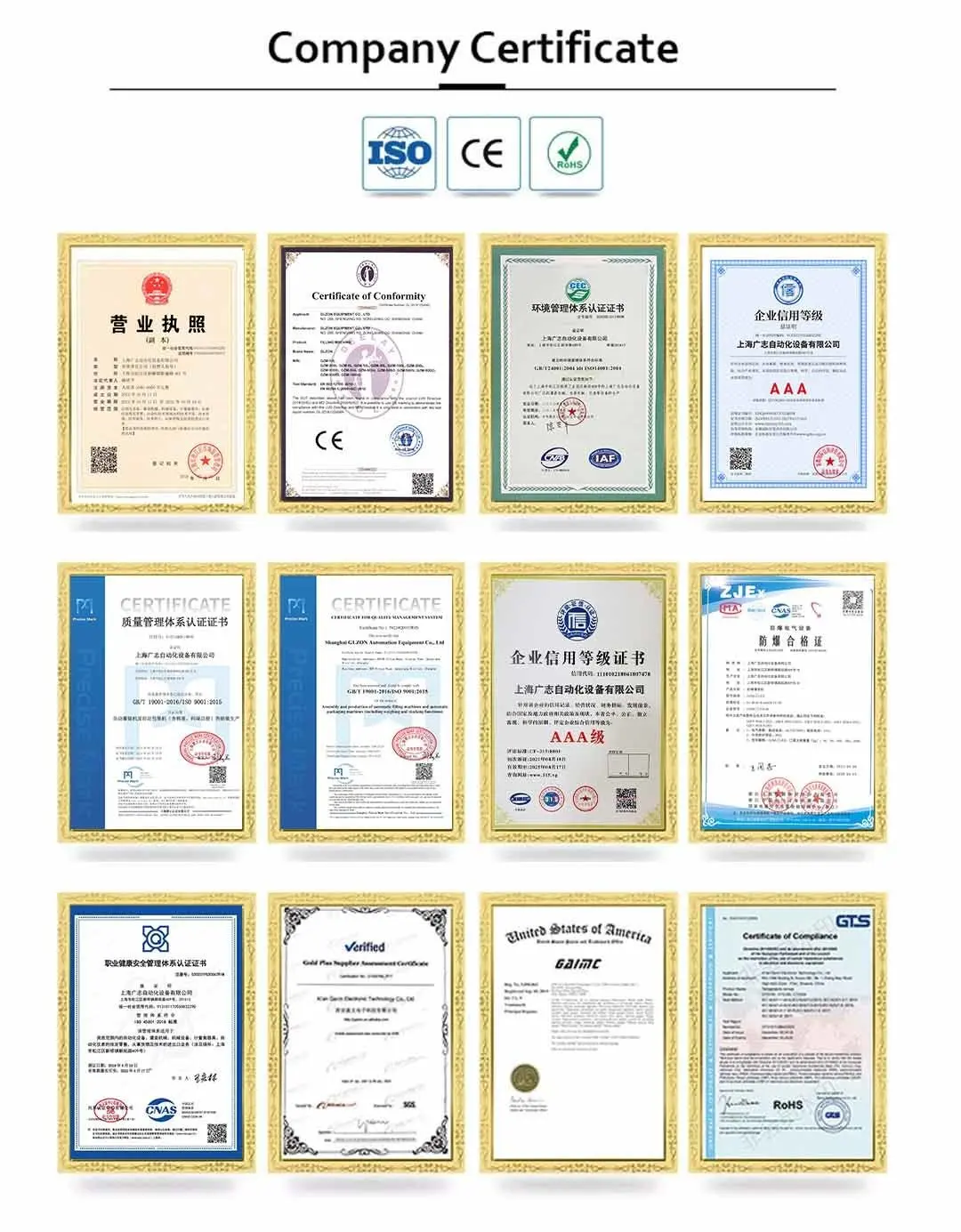
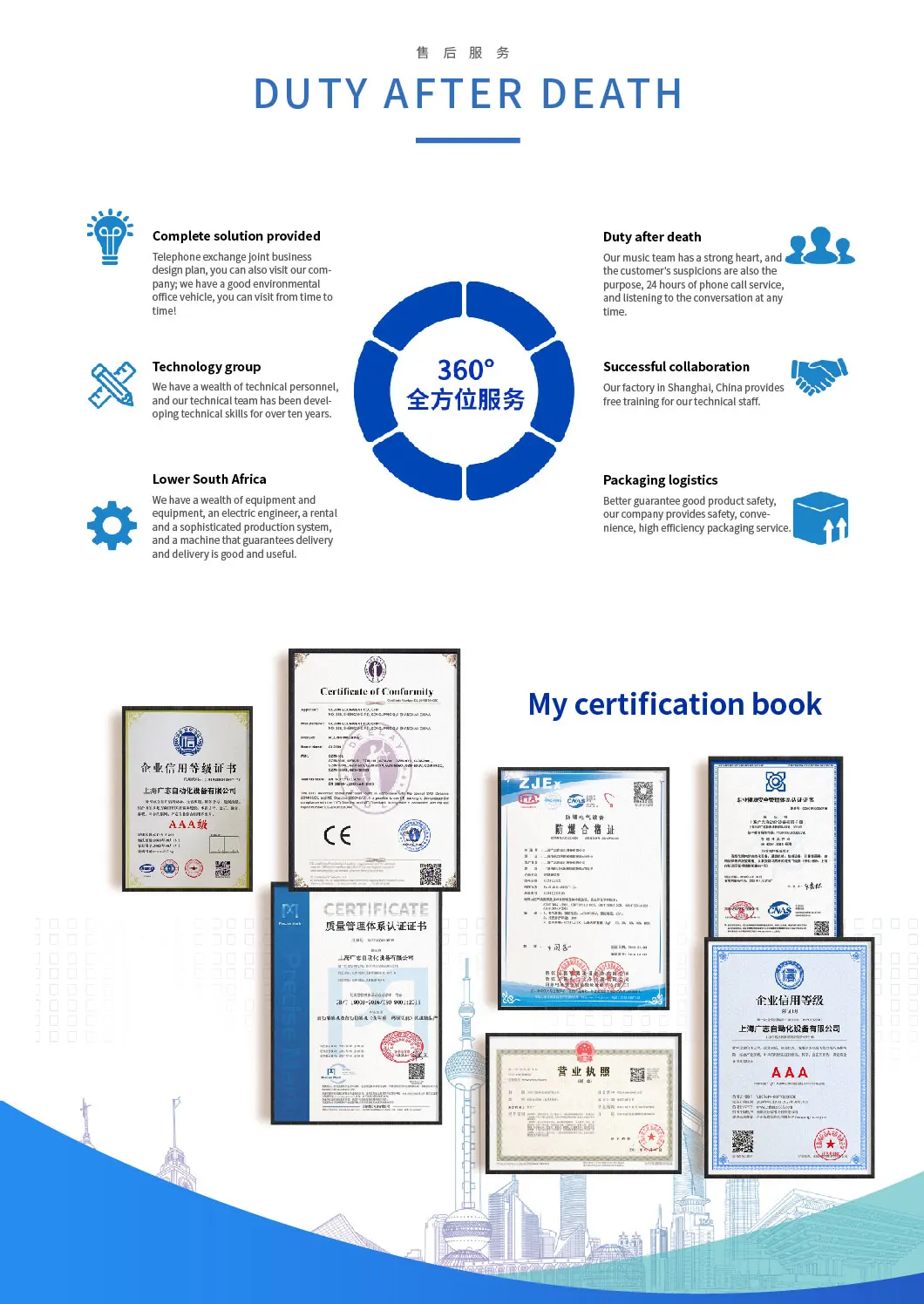
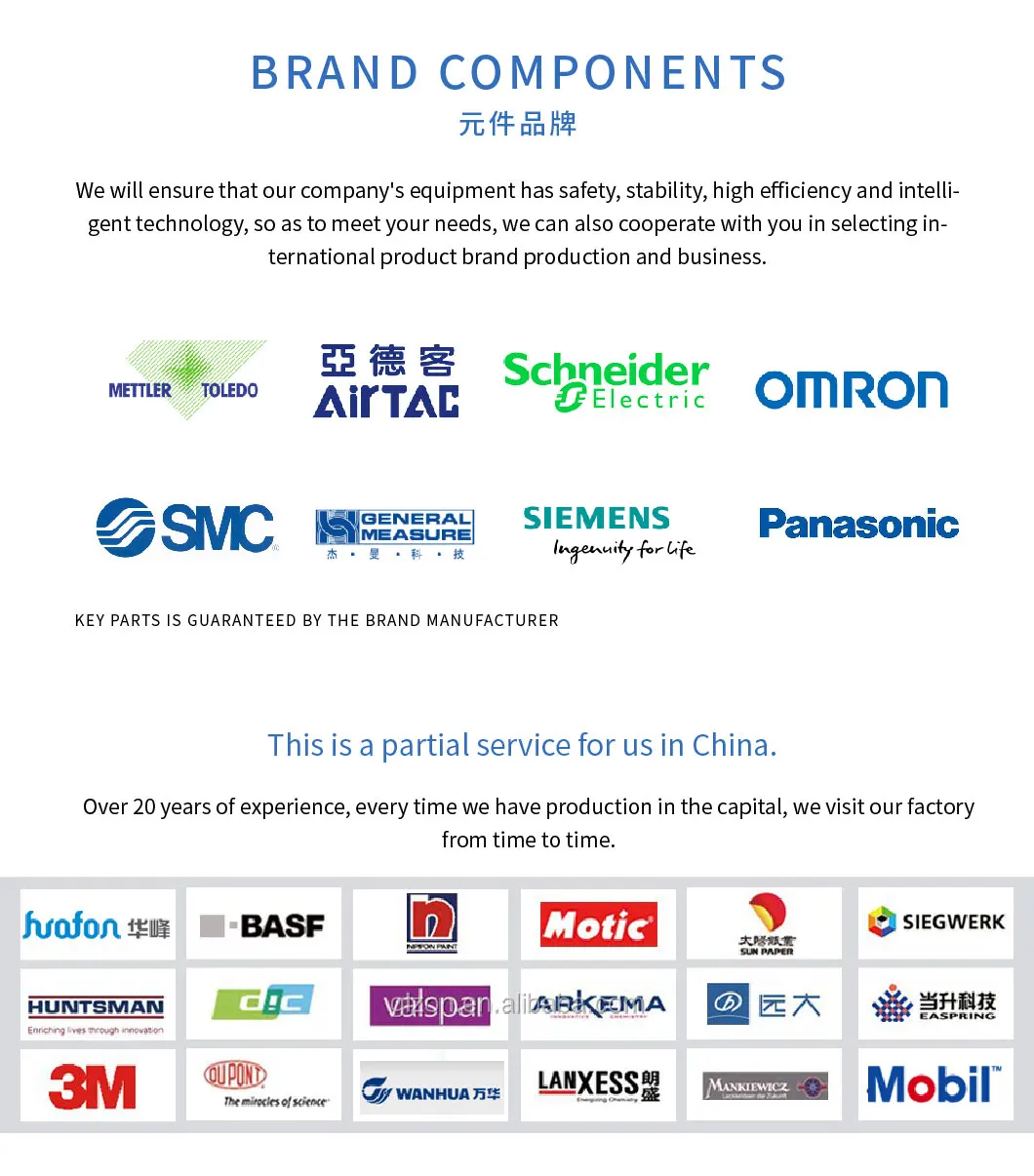
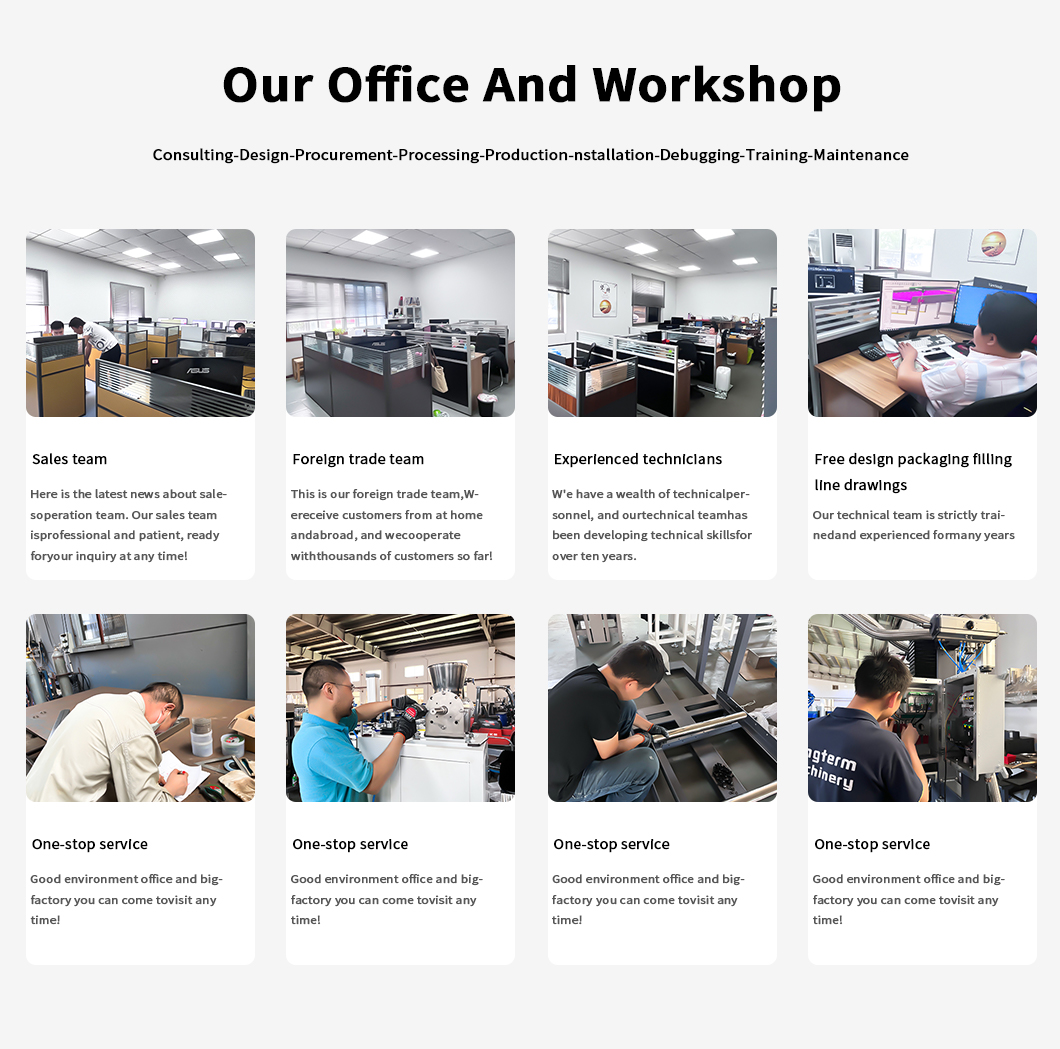
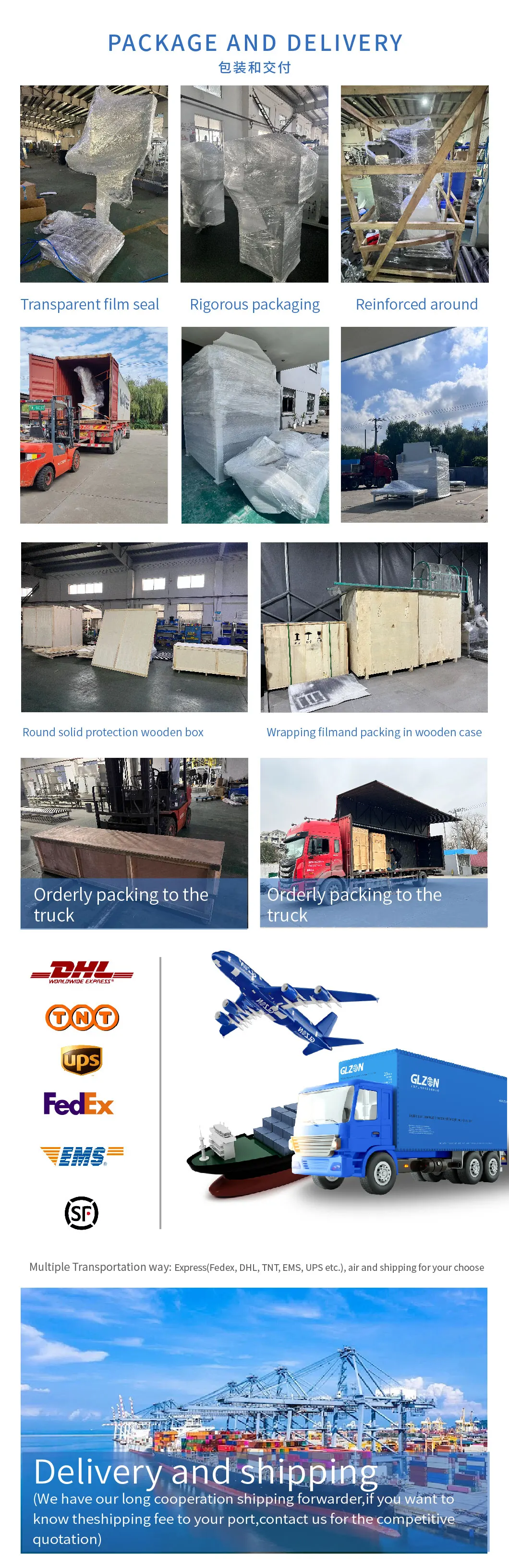
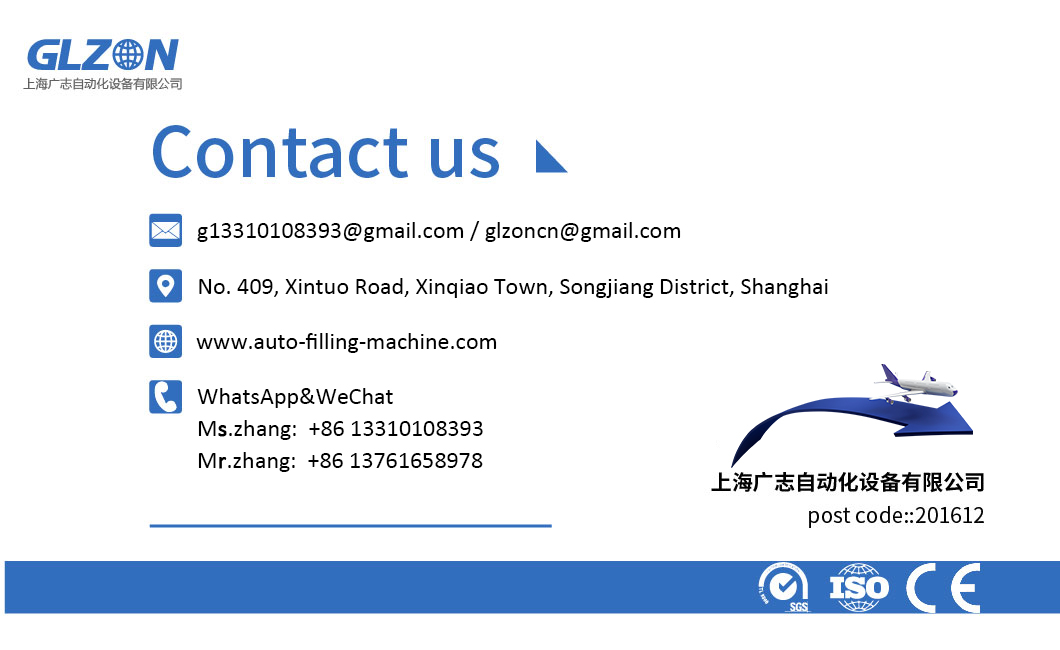